Search
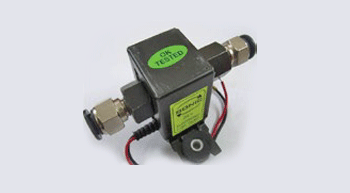
Electronic fuel pump
Sonic Fuel Components is a manufacturer of a wide range of electronic, electrical, and mechanical fuel feed pumps. The fuel feed pumps are manufactured using SS springs, CRCA sheet metal, viton valves, flange gaskets and other high quality raw material.
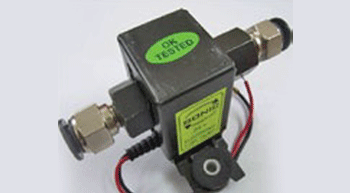
Electronic fuel pump
Sonic Fuel Components is a manufacturer of a wide range of electronic, electrical, and mechanical fuel feed pumps. The fuel feed pumps are manufactured using SS springs, CRCA sheet metal, viton valves, flange gaskets and other high quality raw material.